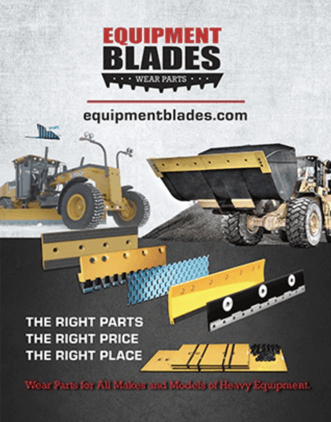
The word "cutting edges" is important in the world of industrial equipment. These cutting edges are the hidden heroes responsible for swiftly slicing through the hardest materials, whether in construction, mining, or agriculture. Not all cutting edges, however, are made equal.
The choice of steel is critical to extending longevity and improving performance. In this post, we'll look at why harder steel is the best option for your cutting edges, as well as the relevance of Brinell hardness and its effect on durability.
Understanding the Different Steel Types
One categorization stands out significantly in the world of steel: AR steel is an abbreviation for abrasion-resistant steel. AR steels are known for their hardness thanks to a thorough hardening process, with Brinell scale readings acting as the final judgment. It should be noted that mild steel lacks the carbon content required for hardening.
High-carbon steel, on the other hand, may be hardened, which results in a higher Brinell rating. This higher grade corresponds to a cutting edge that outlasts its mild steel rivals.
The Surface Hardening Puzzle
While conventional OEM cutting blades may have hardnesses in the 420-450 Brinell range, there's more to it than meets the eye. Surface hardening is often the focus of the hardening process, which means that when the cutting edges wear down, the steel underneath softens, resulting in faster wear and lower lifetime. This is why switching a set of cutting edges generally results in a reduced lifetime.
Hardox Steel Improves Performance
For consumers looking for better cutting-edge performance, SSAB's Hardox steel is an appealing option. Hardox is available in a variety of Brinell grades, with Hardox 500 being an excellent example. You can match the size and thickness of OEM steel while enjoying two to three times the wear life by constructing cutting edges from Hardox 500.
The answer is in the steel's higher Brinell rating, which was obtained by an effective hardening process that ensured a constant hardness level throughout the steel. In fact, SSAB guarantees a minimum of 90% hardness all the way through the steel, ensuring even wear life across the full duration of the cutting edges.
Superior Steel Provides Cost Savings
The advantages of using tougher steel go beyond improved performance. Choosing Hardox or comparable materials saves money on hardware and cutting-edge replacements. In the long term, this means fewer visits to the shop for downtime and edge swaps, which saves money on both labor and downtime.
Increasing Wear Life
Consider changing the size of your cutting edges to increase their wear life even more. While you can't construct them much longer than the bucket allows, you may play with the thickness and surface area. Increasing thickness is an obvious option for increasing wear life, but increasing surface area while retaining thickness may improve the durability of your cutting blades even more.
Conclusion
The choice of steel may make all the difference in the world of cutting blades. Steel with a higher Brinell grade has greater durability and even wear during its lifetime. By using better materials such as Hardox, you not only save money on hardware and replacements, but you also save downtime, which ultimately improves your bottom line.
When it comes to cutting edges, remember that they are more than just tools; they are the lifeblood of your operations, and selecting tougher steel is the key to unlocking their full potential.